Innovations in Cassava Processing
Mozambique Case Study
Bert Dijkink and Jan Broeze
Wageningen Food & Biobased Research CGIAR Research Program on Climate Change, Agriculture and Food Security (CCAFS)Cassava provides food security in many sub-Sahara African countries, as the crop grows year-round and can be harvested at times when other crops are not available. Cassava is traditionally processed to gari (fermented cassava flour) at the farm for home consumption. Besides gari, cassava can also be processed to cassava cake or cassava flour, which can be used in food processing, like for un-malted grain in beer brewing, replacing maize or rice. Since cassava processing is labor-intensive, the processing can be shifted from the farm to the village and to large factories. However, cassava suffers from a large problem with post-harvest physiological deterioration (PPD) which starts 24h-48h after harvest (Reilly, 2003). This together with the wide scattering of smallholder farmers contributes to difficult sourcing and challenging logistics for industrialization.
To overcome these challenges Dadtco Philafrica (www.dadtco-philafrica.com, Dadtco, 2017) developed a mobile cassava flour factory to process fresh cassava on-farm or nearby, instead of transporting the watery, perishable cassava roots over long distances to a central factory.
In this study the effect of different sizes of industrialization of the cassava processing in Mozambique is evaluated for post-harvest losses (PHL) and Greenhouse Gas (GHG) emissions.
Effect on Post harvest losses
Losses during processing depends on the degree of industrialization. At farmhouse and village processing more than 40% of dry weight is lost, mainly during pressing of the cake (IITA 1996).
In mechanical processing (with high speed centrifuges) in a centralised plant, this processing loss is largely reduced. However, this win is counterbalanced by an increase of rejects due to PPD (related to the logistic challenges).
Both inefficiencies can be minimised through a mobile processing unit that is operated close by the production area and produces a more stable product than the crop: either a cake or a dried flour.
Fig 1. illustrates the large reduction of losses due to the introduction of the mobile processing unit.
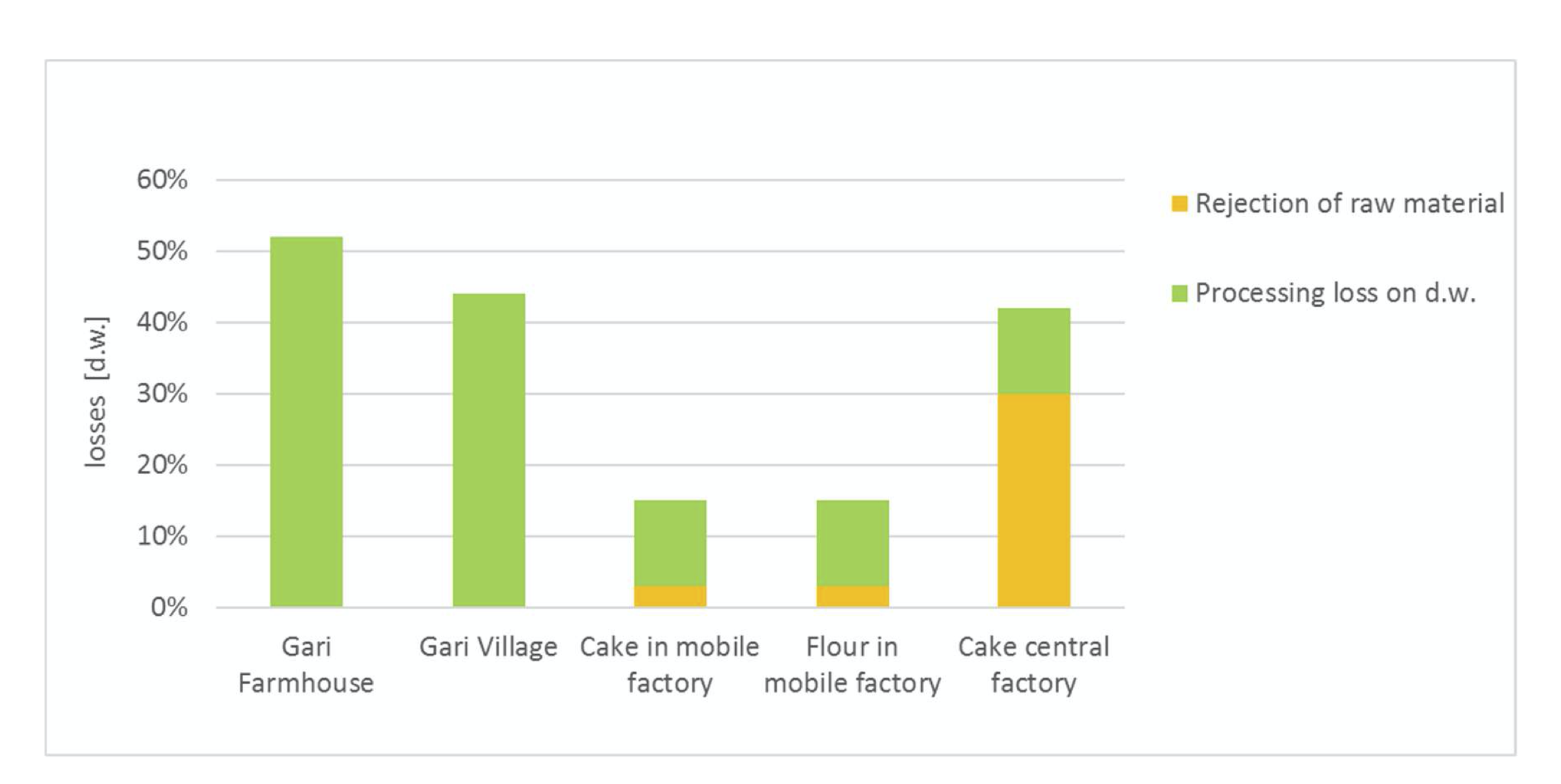
Effect on carbon footprint
GHG gas emissions for processed Cassava (cake or flour) are due to agricultural production (including fuel and optional fertilisers and chemicals use), transport and energy use in processing. Furthermore, losses affect the total efficiency of the chain, and thus increase the total emissions attributed to the usable end-product. The total effects were estimated by means of the Agro-Chain Greenhouse gas Emissions (ACGE) calculator (Broeze, 2019).
Figure 1 shows the estimated total GHG emissions for the different ways of processing, expressed per kg available starch in the end product. Despite the large loss of product during farmhouse or village processing, these pathways are most efficient in terms of GHG emissions. This is due to the relatively low GHG emissions of agricultural production of cassava in the sub-Sahara region (Porter, 2016). The scenarios with mobile mechanical cassava processing have lower net GHG efficiency due to transport and processing energy use. In the comparison of wet cake and dry flour scenarios, the higher energy use in drying is largely compensated for by the more efficient transport.
The reference product, imported maize, induces higher emissions than the mobile cassava processing scenarios. This is due to substantial use of fertilisers and mechanisation in the agricultural production and longer transport distances of the imported product.
The central factory has highest emission results. This is due to the relatively inefficient transport (high-moisture product) and high reject rate at the factory.
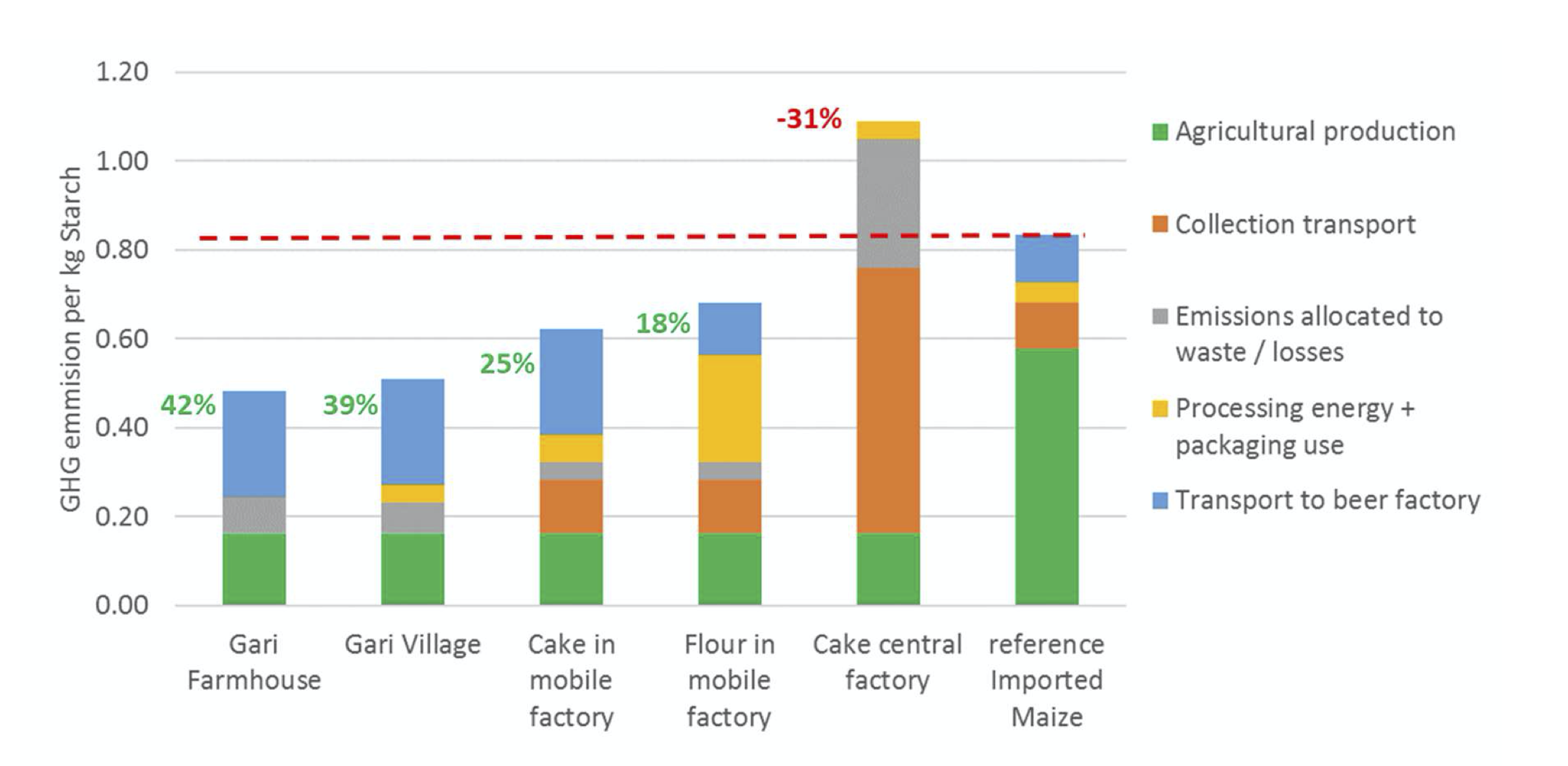
Conclusions
The comparison of three chain configurations for starch supply to a factory shows that for a highly perishable product like cassava a mobile factory that processes the crop to a stable product contributes to loss reduction and reduction of GHG emissions compared to imported starch material and compared to a large-scale central factory. Such a central factory in Mozambique has limited benefits on losses and even results in higher GHG emissions than for the imported starch material.
Acknowledgment
This work is implemented as part of the Consultative Group on International Agricultural Research (CGIAR) Research Program on Climate Change, Agriculture and Food Security (CCAFS), which is carried out with support from CGIAR Fund Donors and through bilateral funding agreements.
References
Broeze, J., et al., A systemic approach for trade-off analysis of food loss reduction and greenhouse gas emissions. CCAFS Working Paper no. XX. 2019. Wageningen, the Netherlands: CGIAR Research Program on Climate Change, Agriculture and Food Security (CCAFS).
Dadtco (2017) Interview Peter Bolt, director and Suzanne Vlakveld cassava value chain manager, Dadtco-philafrica, www.dadtco.nl
IITA. (1996). Improving Postharvest Systems: Archival Report, Crop Improvement Division. International Institute of Tropical Agriculture. Ibadan, Nigeria.
Porter, S.D., D.S. Reay, P. Higgins, E. Bomberg (2016): A half-century of production-phase greenhouse gas emissions from food loss & waste in the global food supply chain, Sci. Total Environ., 571, pp. 721-729.
Reilly, K., R. Gomez-Vasquez, H. Buschman, J. Tohme, and J.R. Beeching (2003). Oxidative stress responses during cassava post-harvest physiological deterioration. Plant Mol. Biol. 53:669–685.